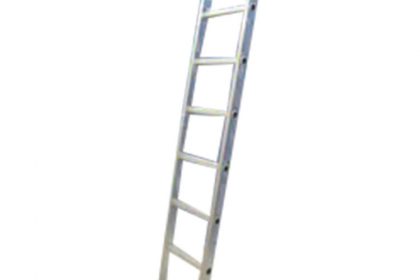
One of the key factors that contribute to the structural integrity of marine ladders is the material used in their construction. Ship ladders are typically made from materials such as steel, aluminum, or fiberglass. Each material has its own set of strengths and weaknesses in terms of durability, weight, and corrosion resistance. Steel ladders are known for their strength and durability, but they can be prone to rust and corrosion when exposed to saltwater. Aluminum ladders are lighter in weight and resistant to corrosion, but they may not be as strong as steel ladders. Fiberglass ladders are lightweight, non-conductive, and corrosion-resistant, making them ideal for use in marine environments.
In addition to the material used, the design and construction of marine ladders also play a crucial role in their structural integrity. Ship ladders must be designed to withstand the dynamic forces and vibrations experienced at sea, as well as the weight and movement of crew members and equipment. The ladder rungs, treads, and handrails must be securely fastened to the ladder frame to ensure stability and prevent accidents. Proper welding, bolting, and other fastening techniques are essential to the strength and durability of ship ladders.
Regular inspection and maintenance are key to ensuring the long-term durability of ship ladders. Inspections should be carried out to detect any signs of wear, corrosion, or damage to the ladder components. Any defects should be repaired promptly to prevent structural failure and ensure the safety of crew members and pilots using the ladder. Routine maintenance tasks such as cleaning, lubricating moving parts, and repainting can help extend the lifespan of ship ladders and prevent premature deterioration.