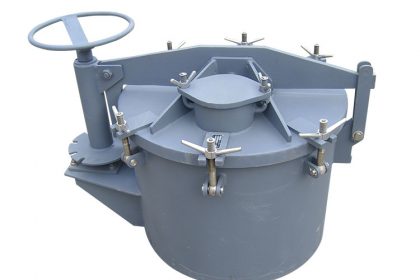
Ensuring the waterproof performance of ship covers is essential for protecting the cargo and maintaining the structural integrity of the ship. There are several measures that can be taken to achieve this.
Material selection: The choice of material for ship covers is crucial in ensuring their waterproof performance. Heavy-duty, waterproof fabrics such as PVC-coated polyester, neoprene-coated nylon, and rubberized canvas are commonly used for ship covers. These materials have high tensile strength and are resistant to punctures and tears. Additionally, they have excellent water-repellent properties, ensuring that water does not seep through the fabric.
Seam sealing: The seams of ship covers are potential weak points where water can infiltrate. To prevent this, it is important to use appropriate seam sealing techniques. Welded seams or heat-sealed seams are preferable as they create a continuous, impermeable barrier against water. Reinforcing the seams with double-stitching or using tapes or adhesives designed for waterproofing can also enhance the waterproof performance of the covers.
Proper fit and tension: Ship covers should be tailored to fit the specific dimensions and contours of the ship. A good fit ensures that there are no gaps or loose areas through which water can enter. Additionally, the covers should be tightly secured and tensioned to prevent sagging or flapping, which can create opportunities for water to accumulate and penetrate the cover. Using adjustable straps, buckles, or bungee cords can help achieve the necessary tension.
Ensuring the waterproof performance of ship covers is crucial for the protection of cargo and the integrity of the ship. Proper material selection, seam sealing techniques, a proper fit and tension, regular inspection and maintenance, testing and certification, and continuous innovation are essential factors to consider. By implementing these measures, ship owners and operators can minimize the risk of water damage and ensure the safe and efficient transportation of goods.